5-Axis CNC Machining: The Definitive Solution for Turbocharger Impeller Fabrication
Precision Engineering for Extreme Performance
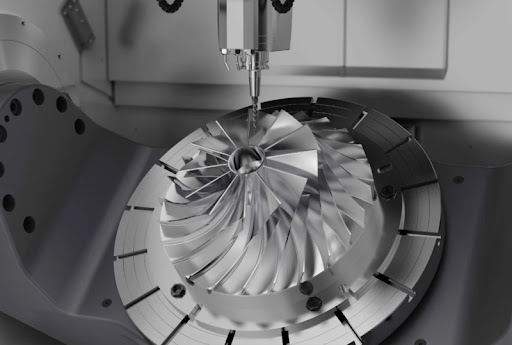
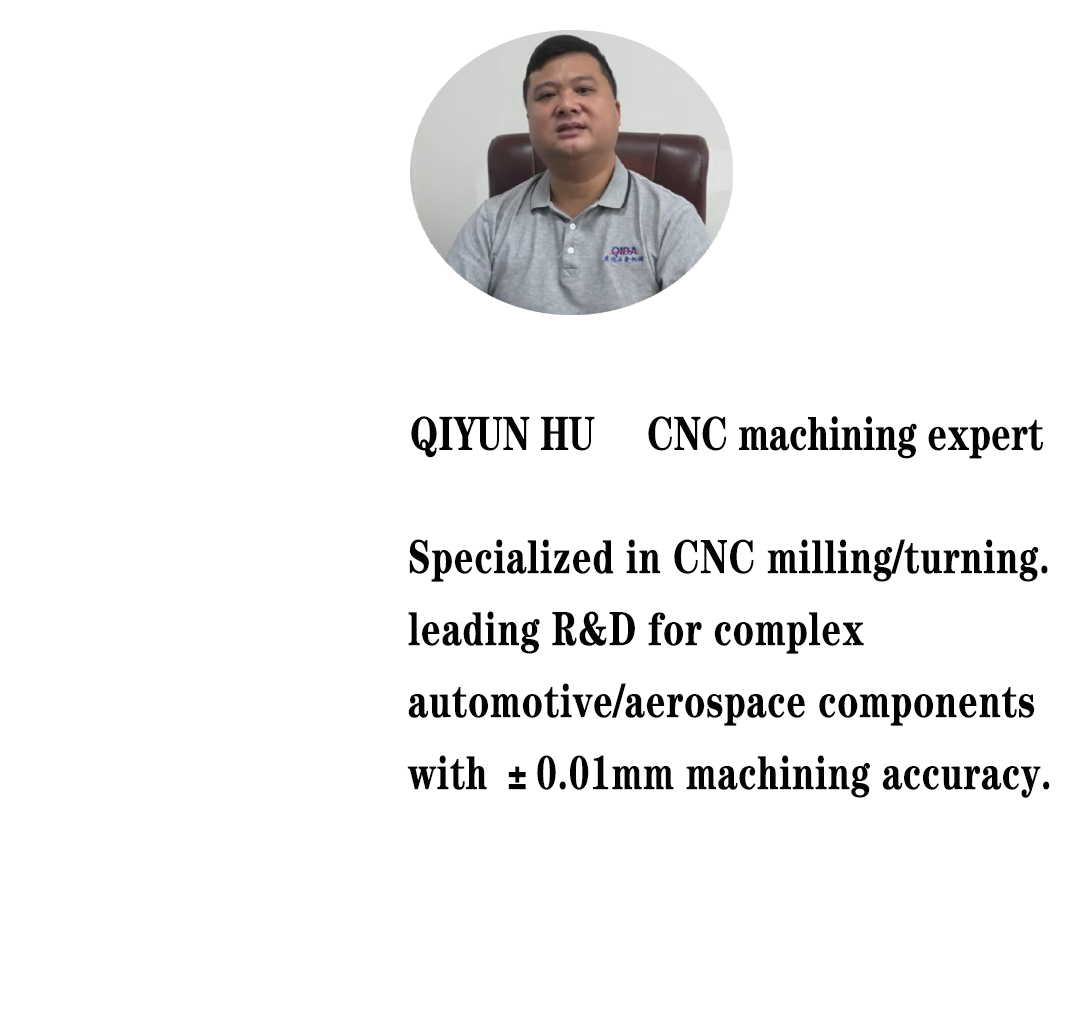
1. Technical Evolution in Turbomachinery
1.1 Industry Demands
- Sub-micron Precision Requirements
- Blade twist angles: 12°–35° (aerodynamic optimization)
- Thermal stability: >900°C operational temperatures (Inconel 718)
- Conflict Resolution
- Thin-wall structures (<0.8mm shroud thickness)
- Complex curvature radii (<2mm)
1.2 Traditional 3-Axis Limitations
Limitation | Impact |
---|
Setup complexity | 8–12 repositioning steps/impeller |
Material waste | 30–40% due to inaccessible regions |
Cumulative errors | ±0.05mm positional deviation |
2. 5-Axis Machining Technology Breakthrough
2.1 Kinematic Advantages
- Simultaneous Motion Control
- X/Y/Z linear + A/B rotary axes synchronization
- Helical interpolation for blade root blending (transition radius<0.1mm)
- Toolpath Optimization
- Trochoidal Milling:
- 3D spiral paths reduce cutting forces by 40%
- Adaptive clearance angles (3°–15° anti-chatter)
- Single-Setup Machining
- Fixtureless clamping (±0.005mm repeatability)
- Thermal compensation algorithms (±2μm stability)
2.2 Performance Comparison
Parameter | 5-Axis Machining | Traditional 3-Axis |
---|
Setup time | 30% reduction | 8–12 steps |
Surface roughness (Ra) | 0.1–0.4μm | 0.8–1.6μm |
Tool life | 300% extension | Standard carbide tools |
3. Precision Solutions for Critical Challenges
3.1 Thin-Wall Machining Protocol
- Vortex Suppression
- High-pressure coolant injection (1000–1500 psi)
- Chip formation stabilization
- Tool Engineering
- Diamond-coated carbide (10° negative rake angle)
- Tool life extension: 300%
- Real-Time Compensation
- In-process metrology for deformation monitoring
3.2 Surface Finish Enhancement
- Multi-Stage Process
- Roughing (Ra 3.2μm)
- Semi-finishing (Ra 1.6μm)
- Spark-assisted polishing (Ra<0.4μm)
- Non-Contact Inspection
- Confocal chromatic sensors (3D topography mapping)
3.3 Dynamic Balance Assurance
- In-Process Correction
- Real-time balancing during finish machining
- Modal Analysis
- FEA modeling of first 10 vibration modes
4. Case Study: Marine Turbocharger Impeller
4.1 Technical Requirements
Specification | Parameters |
---|
Diameter | 52 inches |
Material | Ti-6Al-4V (880MPa yield) |
Tolerance | ±0.02mm concentricity |
Blade Geometry | 18 backward-curved blades |
4.2 Machining Workflow
- Hybrid Process
- 5-axis roughing (12 cm³/min material removal)
- Electrochemical finishing (Ra 0.1μm)
- Quality Control
- CMM inspection every 3 hours (SPC control)
- CNC offset updates via real-time data
4.3 Performance Results
Metric | Achieved | Industry Standard |
---|
Cycle time | 45% reduction | 8–10 hours |
First-article pass rate | 98.7% | 85–90% |
Turbine efficiency gain | 300% (ISO conditions) | 50–100% typical |
5. Runsom Precision’s Technology Ecosystem
5.1 Manufacturing Infrastructure
- Machinery
- DMG MORI NTX 5-axis (12,000rpm spindles)
- Zeiss Calypso metrology (0.5μm resolution)
- Software
- Siemens NX with turbomachinery post-processors
5.2 Value-Added Services
- Design Support
- Free CFD simulations for DFM optimization
- Cost Reduction
- Material substitution recommendations (e.g., Inconel 625 vs. 718)
- Turnkey Solutions
- On-site assembly and dynamic balancing
6. Actionable Next Steps
- Submit 3D Model
- Upload to XINQIDA Turbocharger Portal
- Receive automated manufacturability analysis
- Get Custom Quote
- Comparative 5-axis vs. 3+2 axis cost analysis
- Lead time estimation within 24 hours
- Technical Consultation
- Contact materials science experts: +86 15015326863