Title: CNC Machining Core Technologies: How Xinqida Precision Redefines Precision Manufacturing
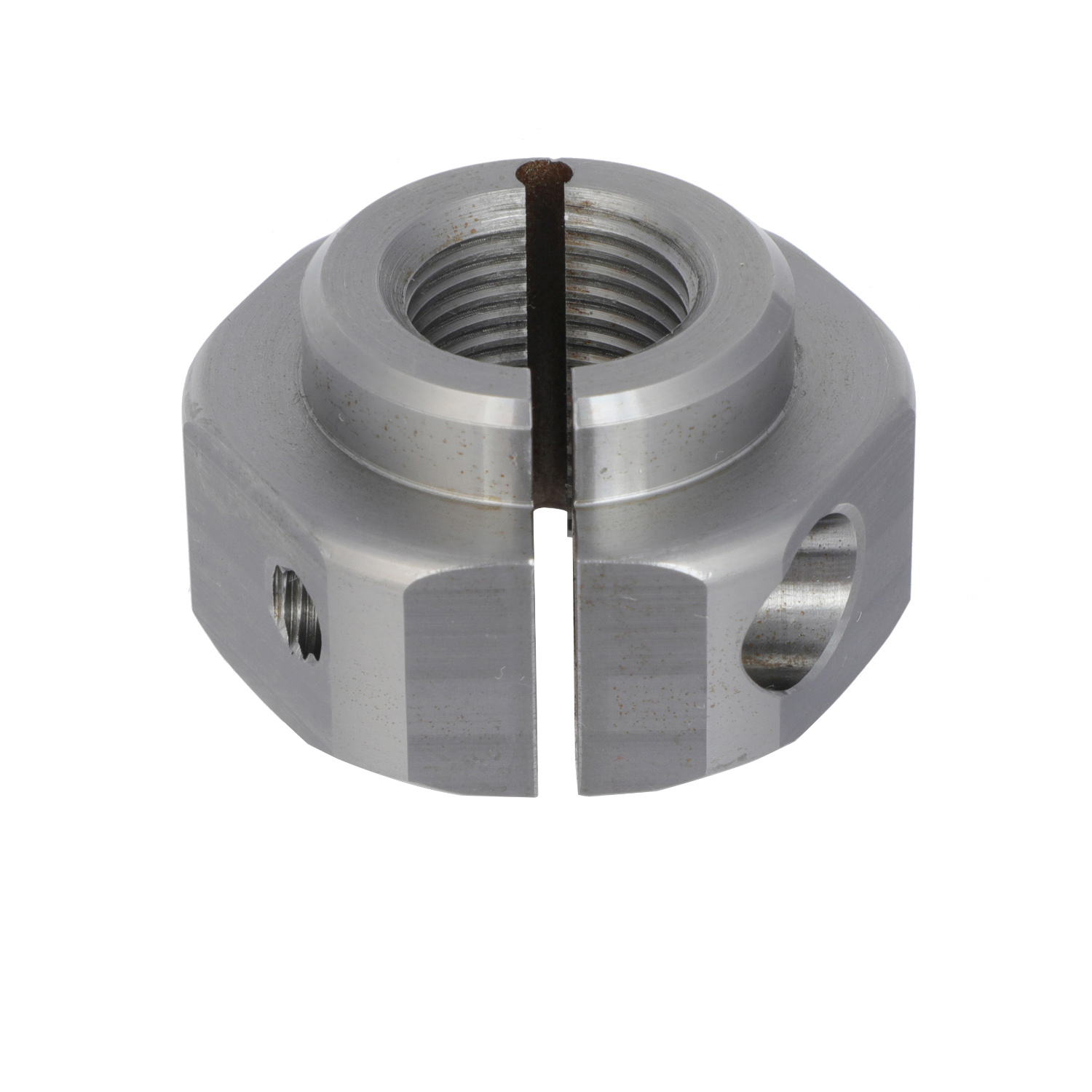
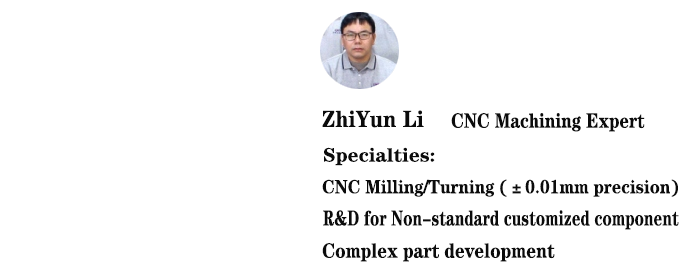
Introduction: The Precision Revolution in Manufacturing
Amid the wave of smart manufacturing, CNC machining has emerged as a core competitiveness in advanced industries. As a pioneer in aluminum alloy processing with 15 years of expertise, Dongguan Xinqida Precision Hardware Accessories Co., Ltd. leverages its five core technology systems to deliver end-to-end solutions for global clients. This article delves into the technical backbone of Xinqida , unveiling its innovation blueprint in precision engineering.
I. CNC Machining Core Technology Matrix
1. High-Precision Machining System
Technical Indicator | Industry Standard | Shenwei Ke Achievement | Application Scenarios |
---|
Positioning Accuracy | ±0.01mm | ±0.002mm | Aerospace precision components |
Surface Roughness | Ra 0.8μm | Ra 0.01μm | Optical lenses/medical implants |
Repeatability | 0.005mm | 0.0005mm | Automotive mass production |
2. Intelligent Process Library
Shenwei Ke’s proprietary CNC Process Database includes:
- 200+ Material Parameters: Aluminum alloys (6061/7075), titanium alloys, stainless steel, etc.
- 1000+ Tooling Solutions: Diamond-coated, PCD composite, ceramic tool combinations.
- 500+ Process Templates: Covering turning/milling/drilling/tapping workflows.
II. Technical Team and Equipment Matrix
1. Expert Technical Team
Core Competency | Certifications | Project Experience |
---|
Complex Surface Programming | Mastercam/UG Advanced Certification | Aerospace turbine blade machining |
In-Machine Measurement | Renishaw Laser Calibration | Satellite component assembly |
Process Optimization | Six Sigma Black Belt Certification | Annual cost-saving projects >300 |
2. Advanced Equipment Cluster
Equipment Type | Model | Key Advantages |
---|
High-Speed Machining Center | DMG MORI CTX Beta 800 | 5-axis linkage / 18,000 rpm spindle |
Precision Turning Center | Okuma LB3000 | Thermal deformation compensation ±0.001mm |
Automated Production Line | Fanuc Robodrill | 72-hour unmanned operation |
III. Quality Control System
1. Full-Lifecycle Inspection
Inspection Stage | Standards | Equipment Configuration |
---|
Incoming Material Check | ISO 2859-1 Sampling Plan | CMM (0.002mm accuracy) |
In-Process Monitoring | SPC Statistical Control | Inline Blue Light Scanning System |
Final Acceptance | MIL-STD-105E Military Spec | Salt Spray Test (48-hour corrosion) |
2. Digital Traceability System
- Blockchain Certification: Unique QR code for each batch, tracing machining parameters, inspector details, and equipment status.
- AI Quality Prediction: Machine learning model identifies 90% potential defects preemptively.
IV. Industry Benchmark Cases
1. New Energy Vehicle Lightweighting
Project Metric | Client Requirement | Shenwei Ke Solution | Outcomes |
---|
Battery Tray Weight Reduction | 30% weight reduction (volume unchanged) | Aluminum microcellular foam structure | Stiffness ↑40% / Cost ↓25% |
Motor Housing Sealing | IP68 Waterproof Rating | Dual-layer vacuum brazing + PTFE coating | Lifetime >10 years |
2. Aerospace Precision Components
Technical Challenge | Solution | Achieved Metrics |
---|
Titanium Alloy Machining | 5-axis linkage + Micro-lubrication | Surface Integrity Ra 0.02μm |
Complex Pipeline Welding | Inertia Friction Welding + Inline Inspection | Weld Strength ≥95% of Base Material |
V. Future Technology Roadmap
1. Three Breakthrough Directions
- Atomic-Scale Machining: Focused Ion Beam (FIB) nanofabrication technology.
- Intelligent Maintenance: Digital twin-based equipment health management system.
- Green Manufacturing: Dry cutting + cutting fluid recycling closed-loop system.
2. Corporate Strategic Upgrades
- Capacity Expansion: Build South China’s largest aluminum machining center (10 million units/year by 2025).
- Industry-Academia Collaboration: Establish “Advanced Manufacturing Joint Lab” with Harbin Institute of Technology.
- Global Footprint: Set up technical service center in Frankfurt, Germany.
Conclusion: Redefining Precision Boundaries
From automotive wheels to satellite components, from smartphone casings to aerospace engines, Shenwei Ke Precision stands at the forefront of CNC machining innovation. Through cutting-edge technology + exceptional service, we have delivered customized solutions to over 300 global enterprises.
Take Action Now
Scan the QR code to download the CNC Machining Technology White Paper, or call +86 150-153-26863 to embark on your precision journey!
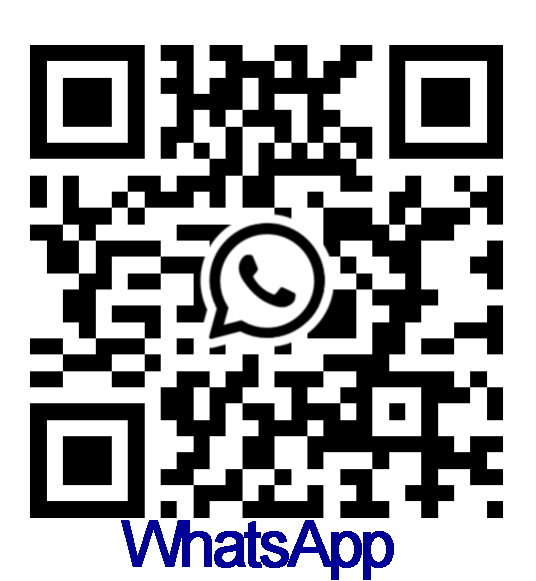