Title: Mastering Aluminum Alloy Machining: A Comprehensive Guide to Techniques and Applications
Source:Dongguan Xinqida Precision Hardware Accessories Co., Ltd. | Published Date: May 30, 2024
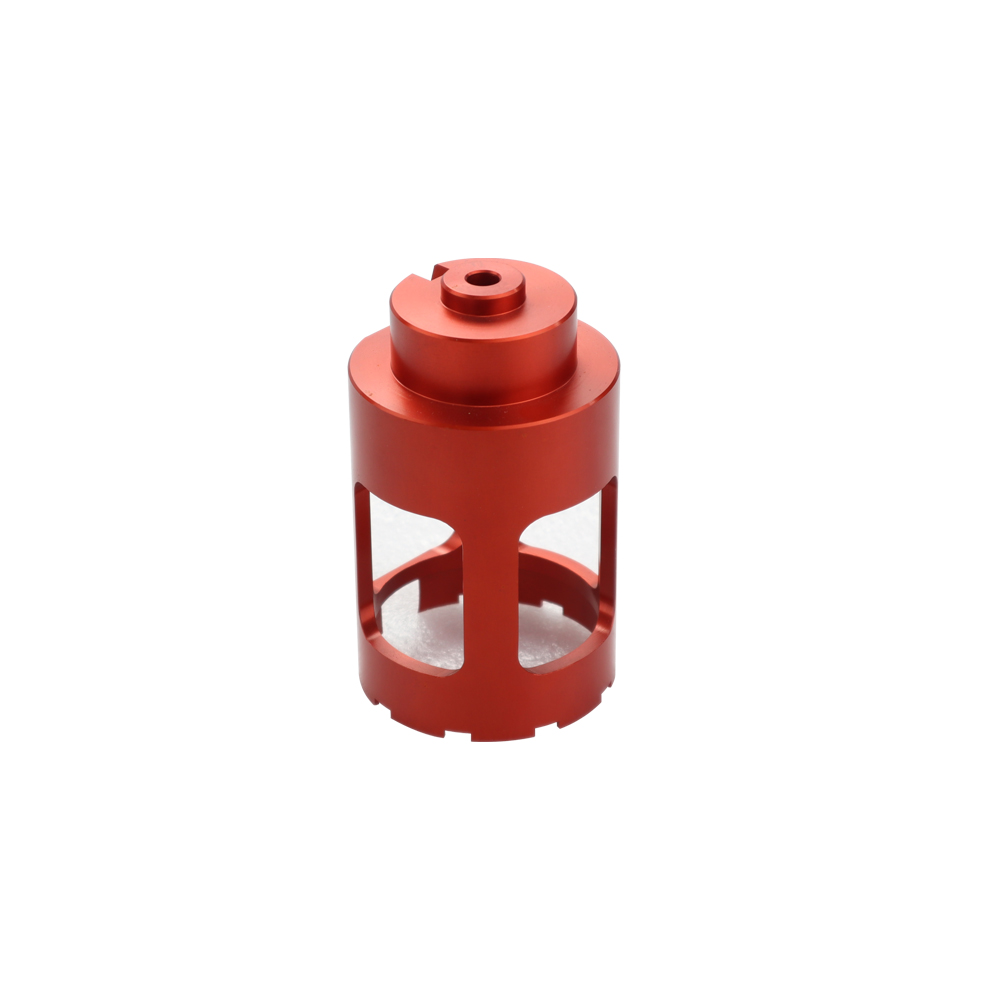
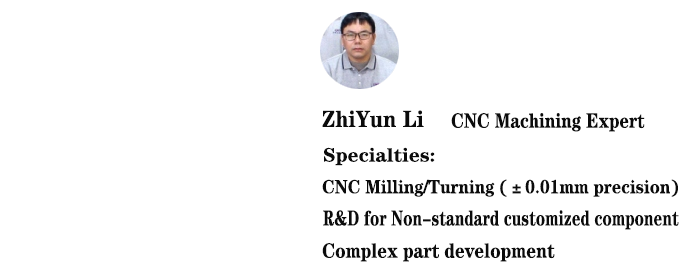
Introduction: Why Aluminum Alloy is the "New Favorite" in Manufacturing?
With the explosive growth of lightweight and high-strength demands, aluminum alloy has rapidly dominated industries such as aerospace, new energy vehicles, and 3C electronics, thanks to its low density (2.7g/cm³), high specific strength (close to steel), and corrosion resistance. However, its machining complexity far exceeds that of ordinary steel. This article delves into the material characteristics, technological challenges, and solutions in aluminum alloy machining to uncover its secrets.
I. Comprehensive Overview of Aluminum Alloy Properties
1. Performance Comparison of Common Grades
Grade | Typical Applications | Tensile Strength (MPa) | Thermal Expansion Coefficient (×10⁻⁶/K) | Machining Difficulty* |
---|
6061 | Automotive wheels/drone frames | 270-300 | 23.6 | ★★☆ |
7075 | Aerospace structural parts | 550-620 | 23.8 | ★★★★☆ |
5052 | Marine equipment/communication base stations | 210-240 | 23.8 | ★★☆ |
2024 | High-strength casings | 470-510 | 23.2 | ★★★☆☆ |
Note: Machining difficulty coefficient based on tool wear rate and surface roughness
2. Processing Contradictions
Feature | Advantage | Challenge |
---|
High thermal conductivity | Suppresses thermal deformation | Prone to tool wear, difficult temperature control |
Low melting point (660℃) | Easy casting | Prone to built-up edge, chip adhesion |
High ductility | Easy forming | Fluctuating cutting forces, poor dimensional stability |
II. Five Core Technological Barriers in Aluminum Alloy Machining
1. Tool Selection Matrix
Tool Material | Application Scenario | Lifespan vs. Cemented Carbide (Baseline) |
---|
CVD Diamond Coating | Mirror finishing (Ra<0.4μm) | 5-8× longer lifespan |
PCD Composite | High-speed cutting (Vc>500m/min) | 3-5× longer lifespan |
Coated Cemented Carbide | General-purpose machining | 1.5-2× longer lifespan |
2. Cutting Parameter Gold Zone
Process Parameter | Recommended Value | Limit Value | Risk Alert |
---|
Cutting Speed (Vc) | 300-450 m/min | >600 m/min (sharp tool wear) | Vibration/chip adhesion |
Feed Rate (f) | 0.15-0.3 mm/r | >0.4 mm/r (surface degradation) | Built-up edge formation |
Depth of Cut (ap) | 0.5-2 mm (roughing) | >3 mm (overload risk) | Spindle vibration/power overload |
3. Cooling Lubrication Innovations
Technology Approach | Coolant Medium | Performance Enhancement | Cost Impact |
---|
Minimum Quantity Lubrication (MQL) | Plant-based nano-emulsion | Temperature ↓35% | +$0.5/part |
Aerosol Cooling | Compressed air + fine oil mist | Chip evacuation ↑40% | $15,000 equipment retrofit |
Cryogenic Machining | -196℃ liquid nitrogen | Tool life ↑200% | +$8-12/part |
III. Industry Benchmark Case Studies
1. New Energy Vehicle Battery Tray Machining
Machining Challenge | Solution | Outcome |
---|
Large thin-wall deformation | Hot forming + vacuum clamping | Flatness error <0.05mm |
Complex surface polishing | CNC milling + magnetorheological finishing | Ra 0.08μm |
Corrosion resistance | Anodizing + PTFE coating | Salt spray resistance ≥500h |
2. Aerospace Aluminum Forging Precision Machining
Core Metric | Traditional Process Defects | CNC Optimization Solutions |
---|
Roundness tolerance | ±0.05mm (post-machining) | Thermal symmetric clamping + real-time compensation |
Surface integrity | Presence of work-hardened layer | Cryogenic cutting + MQL |
Batch consistency | CPK value 1.23 (unstable) | Digital twin modeling + SPC control |
IV. Future Trends: Intelligence Meets Sustainability
1. Technological Disruptions
- Adaptive Machining Systems: AI-driven parameter adjustment (response time<1ms)
- Hybrid Machining: Integration of turning, milling, and grinding (efficiency ↑60%)
- Green Machining: Commercialization of zero-emission dry cutting
2. Corporate Strategy Recommendations
- Process Database Development: Build a cutting parameter library for 200+ alloys
- Tool Lifecycle Management: RFID-enabled tool wear tracking (accuracy >95%)
- Production Line Flexibility: Quick-change fixture systems (tooling swap in<3 minutes)
Conclusion: Unlocking the "Secret Code" of Aluminum Alloy Machining
From material properties to process innovation, from cost control to green manufacturing, aluminum alloy machining has evolved into a sophisticated knowledge system. Shenzhen XW-Tech Precision Engineering, with 15 years of industry expertise, has developed an aluminum alloy machining database applied in:
✅ Mass production of lightweight automotive components (5 million units/year)
✅ R&D prototyping of aerospace precision components (±0.005mm precision)
✅ 5G communication heat dissipation modules (Ra 0.01μm surface finish)
Take Action Now
Scan the QR code below to download the Aluminum Alloy Machining Parameter Handbook, or call +86 150-153-26863 to unlock your tailored machining solution!
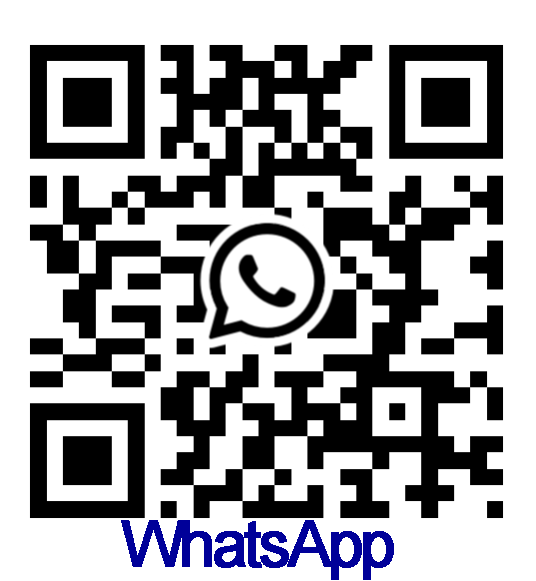